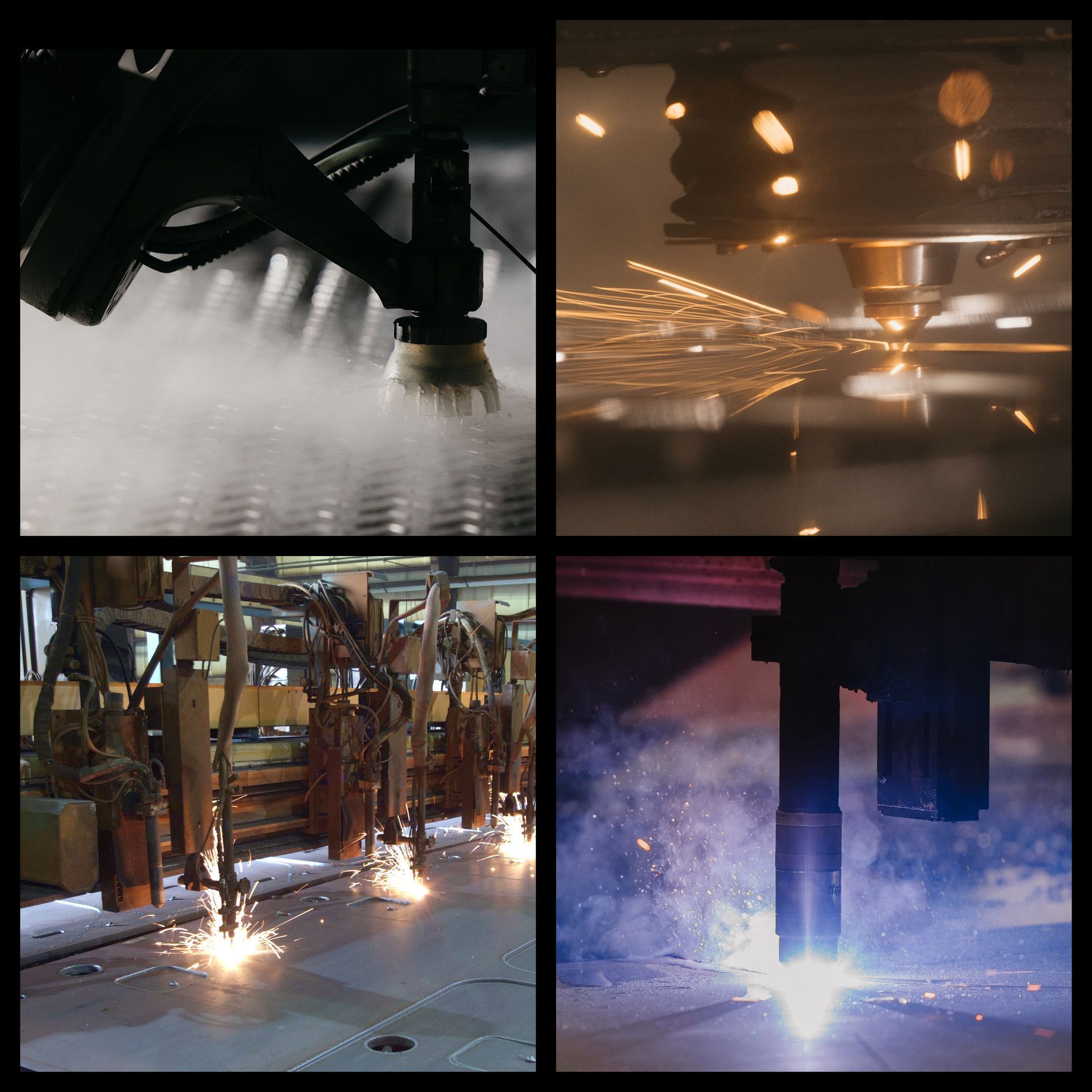
Burning - Fabrication First Ops
Initial cutting operations – or burning – of metal sheet or plate material is often referred to as “1st Ops”, the process that creates basic shapes for further processing.
HISTORY
In 1999, an existing customer, JLG Industries, asked us to start cutting parts for them from raw metal. Olympic Steel bought its first plasma machine and began making usable pieces in the new Chambersburg, PA facility. Since that time, the Company has continued to offer a number of fabrication processes and amassed a nice array of burn tables. Across the Olympic Steel enterprise, there are currently 23 sheet lasers (4.5 to 20kw), 18 tube lasers, 58 plasma/oxy torches and 3 waterjet machines. Operations Managers at the division level handle the daily production and maintenance, while Corporate Operations purchases and sets up equipment and drives standard operating procedures.
BURNING - 1st OPS
In metal fabrication, “1st Ops” refers to the initial burning or cutting of a metal sheet or plate into sizes needed for the final product. It prepares the metal for further processing such as forming, machining or welding. Olympic Steel utilizes 4 of the 5 main types of burning.
- Laser Cutting – Uses a high-powered laser beam (sheet and tube lasers – 2kw-50kw in the U.S.) to precisely cut, engrave or etch metal. The beam is focused on the surface of the metal and intense heat melts or vaporizes the material creating clean, accurate cuts in thicknesses up to 2 inches with tolerances of +/- 0.010 inch.
- Plasma Cutting – Utilizes a high-velocity jet (up to 46 amp) of ionized gas (plasma) to cut through electrically conductive materials, such as carbon and stainless steel, aluminum and copper. An electrical current moves through the gas, which is directed onto the metal surface. The intense heat of the plasma melts the metal, and a jet of gas blows away the molten material, leaving a clean cut in material up to 2.5 inches, holding +/- 0.060 inch tolerances.
- Oxy Fuel Cutting - Uses a mixture of oxygen and a fuel gas (typically acetylene) to create a high-temperature flame, which is directed at the metal, usually steel, to heat to its ignition point. Once the metal reaches the right temperature, a stream of pure oxygen creates a cut by burning and removing the molten metal. Oxy cutting can handle materials up to 10 inches thick and tolerances of +/- 0.060 inch.
- Water Jet Cutting – Employs a high-pressure stream of water, often mixed with an abrasive material, to cut through metals and a wide range of other materials, including stone, glass and plastics. It is capable of creating precise, clean cuts without generating heat, which eliminates the risk of thermal distortion or material hardening. It is particularly useful for intricate designs and parts that require high accuracy in materials up to 2.5 inches maintaining tolerances of +/- 0.005-0.010 inch.
PRODUCTS
Every day, we run across items that have gone through the burning or cutting process. Olympic Steel serves many industries such as construction, food service, heavy machinery, HVAC and agriculture. When you pass a truck trailer on the interstate, see a farm tractor or combine in a field, watch your burger sizzle on a grill in a restaurant, turn up the heat or light the fireplace, mow your lawn, grab a handrail outside your favorite stadium after passing security bollards, and sit in that office chair – you are experiencing the wonder of metal that has gone through fabrication, include a burning process, in its path to be transformed into the final products we see and use each day.
OUTLOOK
Across the Company, there is a strong focus on value-added fabrication services, starting with burning as one of the fundamental first steps. Minimizing waste when nesting parts for cutting, utilizing assets to their fullest extent, and keeping equipment highly functional and updated are all important objectives in support of Olympic Steel’s strategy for safely providing solutions while achieving profitable, sustainable growth.
Learn more about our processes, family of brands, business segments, divisions and subsidiaries at Olympic Steel Academy!