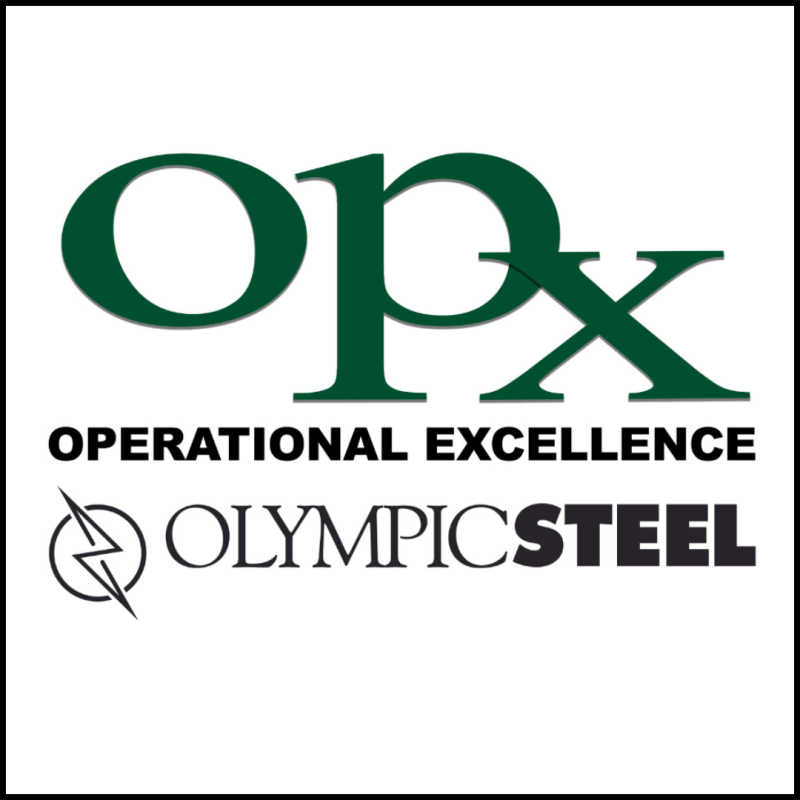
Introducing the Central Region’s Operational Excellence (OpEx) Team
A frequently used resource for the Central Region, the Operational Excellence Team is branching out to help others across the company. Find out who they are and how they can help you and your teams operate more efficiently and effectively.
The Central Region Operational Excellence Team believes “work can be better tomorrow than it was yesterday.” And, they understand that improving is a process that takes time. You might not see results each day, but over time you’ll learn as you go and get a little bit better than you were before.
WHAT IS OPERATIONAL EXCELLENCE?
Operational excellence is our term for project management procedures and practices that utilize lean
six sigma methodologies. Six Sigma provides tools to improve the capability of business processes using the DMAIC approach: Define, Measure, Analyze, Improve, Control. Six Sigma training is divided by project management levels and categorized by colored ‘belts’:
- White Belt – Understands basic six sigma concepts from an awareness perspective; can work on local problem-solving teams that support overall projects but may not be part of a Six Sigma project team.
- Yellow Belt – Participates as a project team member; reviews process improvements that support the project.
- Green Belt – Assists with data collection and analysis for Black Belt projects; leads Green Belt projects or teams.
- Black Belt – Leads problem-solving projects, trains and coaches project teams.
- Master Black Belt
– Trains and coaches Black Belts and Green Belts; functions more at the Six Sigma program level by developing key metrics and strategic direction. Acts as an organization’s Six Sigma internal consultant.
A LITTLE BACKGROUND
Understanding the benefit of lean six sigma methodologies, in 2015 and 2016, Olympic Steel utilized an outside consultant to train two waves of Black Belts. One member of that group was Will Robbins, Sr. Project Analyst and (now) Black Belt for Olympic Steel’s Minneapolis, MN Coil and Plate facilities.
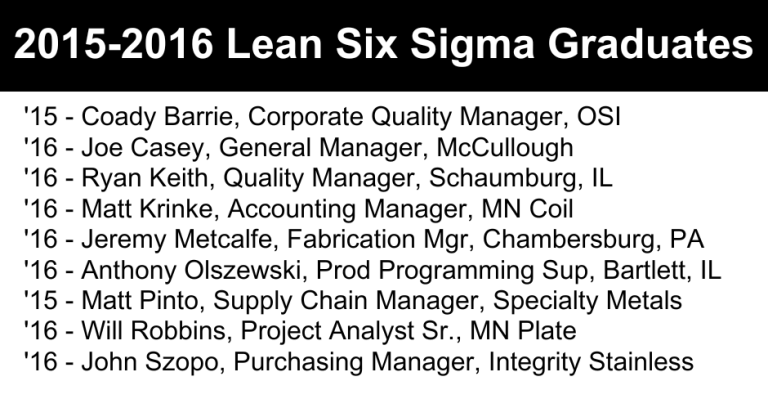
In 2019, Tom Sacco, Central Region Vice President and Minneapolis, MN General Manager, introduced the idea to create an Operational Excellence Team in MN with Robert Erion and Will Robbins. They started projects, interacted with employees, and helped out most departments with projects and initiatives.
“Tom saw the value in black belt projects and understood that Green Belt training wouldn’t be useful without continued direction and support when the employee returns to their ‘day job’,” explains Robert Erion, Master Black Belt and Safety & Project Manager for Olympic Steel’s Minneapolis, MN facilities.
OPERATIONAL EXCELLENCE TODAY
Since 2015, Lean Six Sigma at Olympic Steel has evolved from primarily project-based initiatives to learning methodologies. Operational Excellence can help others learn how to solve their problems and provides the toolkit to do just that. With regional leadership support, Robert and Will began training Green Belts in 2020. Since then, they’ve trained three waves of Green Belts.
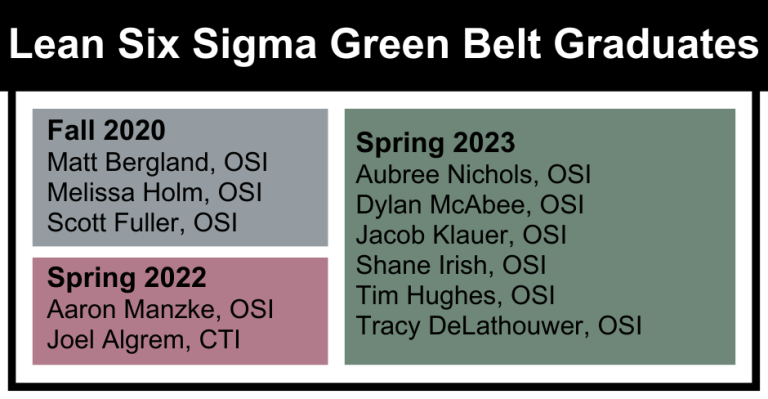
“With each Green Belt class, we’ve changed and improved what we’re doing,” says Robert. “We teach participants that we want tomorrow to be a little bit better than the day before – and we mean it. Learning is a process and results may not be seen immediately, but it doesn’t mean you aren’t making progress and moving in the right direction.”
Will Robbins adds this, “Our vision is to establish Olympic Steel as a learning organization where everyone is capable and empowered to solve their own problems. And that starts with providing the tools and techniques needed to those interested in learning how.”
If you’d like to be considered for Green Belt training, reach out to your General Manager to discuss the process.