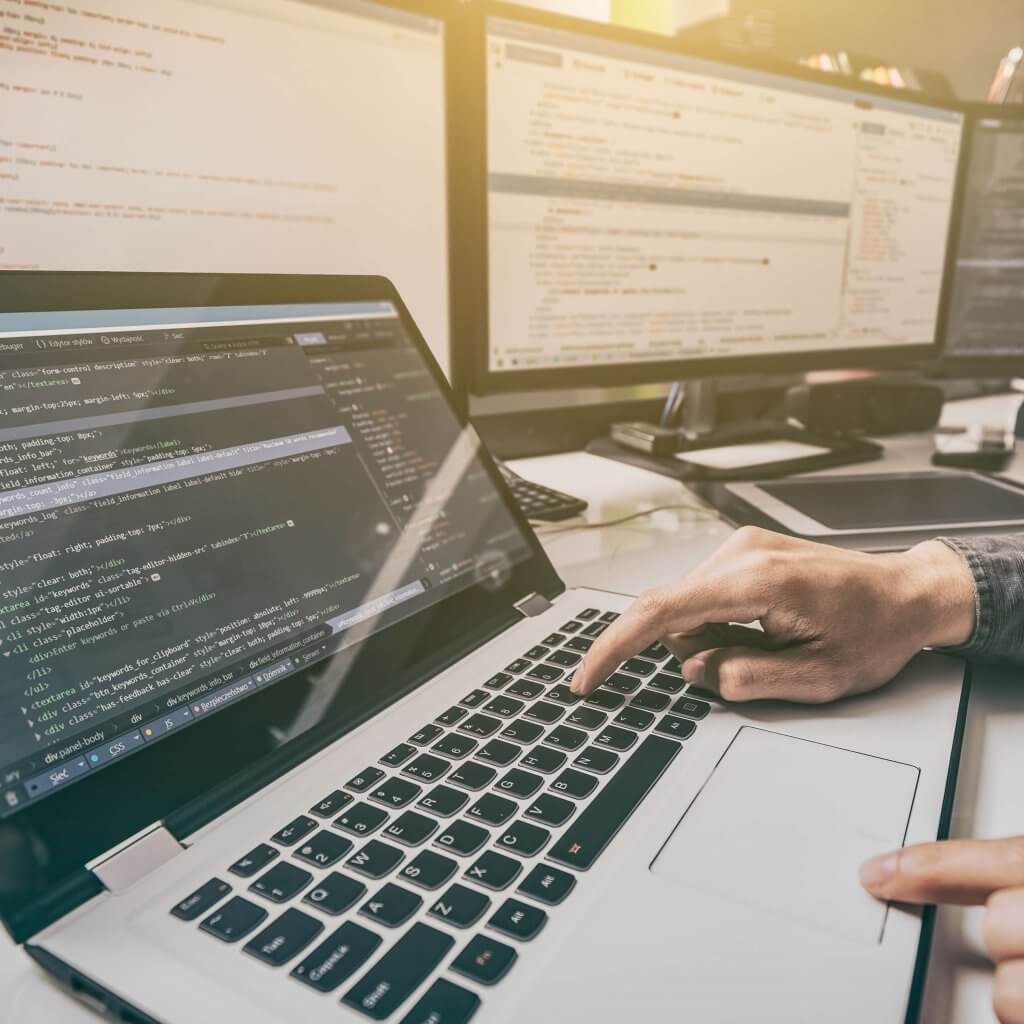
McCullough Industries Completes SEMS Integration
The SEMS implementation was a full team effort by McCullough and Corporate employees, marking a defining moment in SEMS implementation history.
May 1, 2021 marked the twelfth implementation of the SEMS ERP system at an Olympic Steel division.
Larry Lutsko, Manager of Solution Services, and his team of business analysts spent more than six months working with Joe Casey and his team at McCullough Industries, training employees and developing processes and procedures to support the operation.
“It’s been a smooth transition and fantastic to work with IT. In-person and remote training made the transition as easy as could be expected for such a significant change,” says Joe Casey, General Manager at McCullough Industries. “The SEMS system will allow us to focus on growing our business by eliminating barriers imposed by our older system. It was much-needed, and we’re happy to have these new tools.”
Larry Lutsko, Project Manager for the McCullough implementation, was pleased with the collaboration. Said Lutsko, “The McCullough team has been great to work with. All of the team members were very receptive to the changes throughout the training process.”
When asked what surprised him most about the project, Larry said “I was surprised by how well the SEMS solution worked with Bill of Material production to support McCullough’s requirements.”
While the SEMS solution has supported light manufacturing at our Schaumburg division, the McCullough SEMS implementation marks a defining moment in the number of parts, variants and volume of manufactured goods.
Lea Hamilton, Office Manager at McCullough Industries, was involved in all facets of training, including development of new processes and procedures to support the system. Said Hamilton, “The biggest benefit I see so far is the ability to track orders and inventory throughout the system. I can see what’s happening without having to track people down on the plant floor.”
The implementation team at McCullough also includes Bernadine “Bernie” Pieper (Administrative Assistant), Connie Beazley (Traffic Coordinator), Lynn Chute (Traffic Coordinator) and Lucas Schreck (Machine Operator). Each team member identified an area of expertise to keep the transition running smoothly:
- Bernie Pieper – weldment production recording and truck routing
- Connie Beazley – sales order management
- Lynn Chute – shipment planning and scheduling
- Lucas Schreck – a “super user” focusing on plant operations – production planning, scheduling and recording for burning and sawing operations
Despite the complexity of the McCullough process, this implementation has been one of the fastest implementations for the Corporate team. Larry kept costs down by engaging just four highly experienced business analysts:
- Jen Gea supported the sales function, parts and bill of material conversion as well as the sales order migration process
- Patrick Smullen supported shipping, receiving and purchasing
- Rich Carney supported production planning, scheduling and recording, working closely with Lucas, Bernie and Lea
“The McCullough operation is so different from our standard distribution line of business; it made this project intriguing and memorable,” says Jen, who has worked on virtually every SEMS and AX implementation. “The McCullough team members were quick learners and really excited to get on a new system.”
“It was nice to work with people who understand the whole manufacturing and business process,” Rich adds.
The group at McCullough also received support from the rest of the Corporate team including Debbie Jadrych and our software development team and Joe DePascale and our infrastructure team. Marty Hess was on-site to support any last-minute technical infrastructure issues.
“I’m so proud of my team and the McCullough team,” says Chris Garrett, Vice President of Information Services. “The past year has been challenging with travel restrictions and meeting limitations. Everyone pitched in to make this happen quickly and smoothly. When compared to past SEMS implementations, McCullough is a different operation. I’m impressed with how the division and my team figured out how to make it work with minimal enhancements. Undoubtedly, over the next few months, there will be bumps along the way as the McCullough team settles into their new system. My team is ready to help when needed.”
Chris add, “My thanks go out to Joe Casey and his team. Joe’s leadership and direct participation were key to the success of this implementation.”