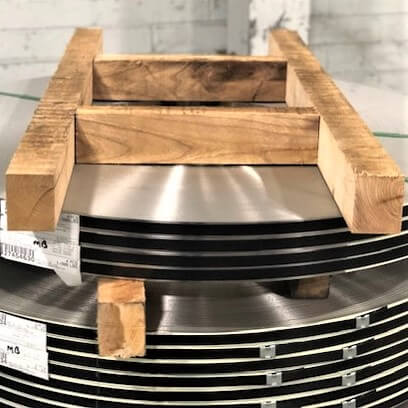
Mistake Proofing with Poka Yoke
Whether big or small, every mistake is an opportunity to learn and improve.
Poka yoke. No, it’s not a video game. Poka yoke (pronounced Poh ka Yoke) is a mistake-proofing approach used to eliminate or prevent errors. The phrase poka yoke is derived from the Japanese word that means ‘to avoid errors’. A poka yoke is simply a way to help avoid mistakes and improve processes.
Since January, six divisions identified NINE ways to eliminate errors – would any of these ideas also work for you or your team?
Olympic Steel – Buford, GA
Moving quicker AND safer with secure storage racks: Freestanding racks at the facility were installed near each other to make pulling parts quicker and easier. After installation, brackets were added to connect the racks, making them sturdier, less likely to move, shift or fall if struck by a lift and therefore, safer.
Olympic Steel – Cleveland, OH
Laser slat storage for a safer workspace: Laser #3 and #6 slats were often stored on the floor nearby when not in use. A team including a Lead, Laser Operators and Maintenance employees designed, fabricated and painted a storage solution to keep the slats organized and off the floor. This in-house solution removed a potential trip hazard and completed 5S in two areas!
Olympic Steel – Dover, OH
An unfortunate event gives fresh perspective on storage: An air compressor fire presented a unique opportunity to look at combustible storage with fresh eyes. The Dover team identified a new storage area and marked off 4’ clearance around the air compressors to visually alert employees that nothing is to be stored within the area.
Integrity Stainless – Latrobe, PA
Near miss provides an opportunity to improve an SOP: When removing a skid of sheets from the CTL chains to the scale/packing station, chain slots make it difficult to keep the load level. A team suggested using two industrial clamps to hold the sheets in place during transport to reduce a potential safety risk.
Laser focus gets the team into a new flow: When running flat-bar material through the edging machine, material to be processed is placed on the table where finished material exits the machine. When rework flat-bar is not far enough from where finished material exits the machine, pieces can collide. A small laser guide was added to the machine, projecting a red line onto the table where the material is kept. The laser line clearly identifies the area where rework material should not be placed to keep rework and finished products from colliding.
Integrity Stainless – Streetsboro, OH
Protecting material and employees drives process improvement: When slitting material, coils can oscillate, creating an uneven side-wall. Boards were installed to protect the side-wall from becoming damaged running down the conveyor from the lay down table, but to place the boards on the machine, an employee would need to bypass a safety device and enter the danger zone. After assessing the process and identifying the hazard, a jig was built that removed the employee from the danger zone.
To minimize risk, consistency is key: Stacked bundles of slit stock are separated by placing two 3” x 4” pieces of wood between each bundle. The wood spacers, if not uniformly positioned, create the potential for the material to fall over. The Safety Team built a jig that consistently places the wood in the same position between each bundle.
Slip-resistant mats for safer, cleaner work stations: Coolant is used when skiving material to keep the cutters from overheating and becoming dull. The coolant can collect on the platform and create a slippery surface where the employee stands. The team assessed the hazard and added a slip-resistant mat to the platform, eliminating the slippery surface.
McCullough Industries – Kenton, OH
Keeping vendors safe with product modifications: Poka yokes don’t have to be for our employees only! Jon Wilson noticed that the Cintas uniform rep had trouble collecting items from the uniform bin. She had to lean over the sides, often with her feet in the air, to reach the contents of the bin. Jon modified the bin with a step for easier access.
Identifying the risk is the first step to eliminating the risk: An operator used their hand to hold a part during the forming process, which put their hand dangerously close to a pinch point. To minimize this risk, a jig was attached to the machine to provide an area for the part to safely lay during the process, removing the need for the employee to hold the part in place.
Every day and every challenge present opportunities to improve. Don’t ever let yourself be the one who says, “Well, that’s how we’ve always done it.”
Has someone at your division mistake-proofed a process?
Do you have a poka yoke to share?
Send an email to Tony.Dominic@olysteel.com to share your division’s best practices to help us set the standard as we all learn and improve together.
And, watch for other great Poka Yoke ideas, published in the Monthly Safety Report.