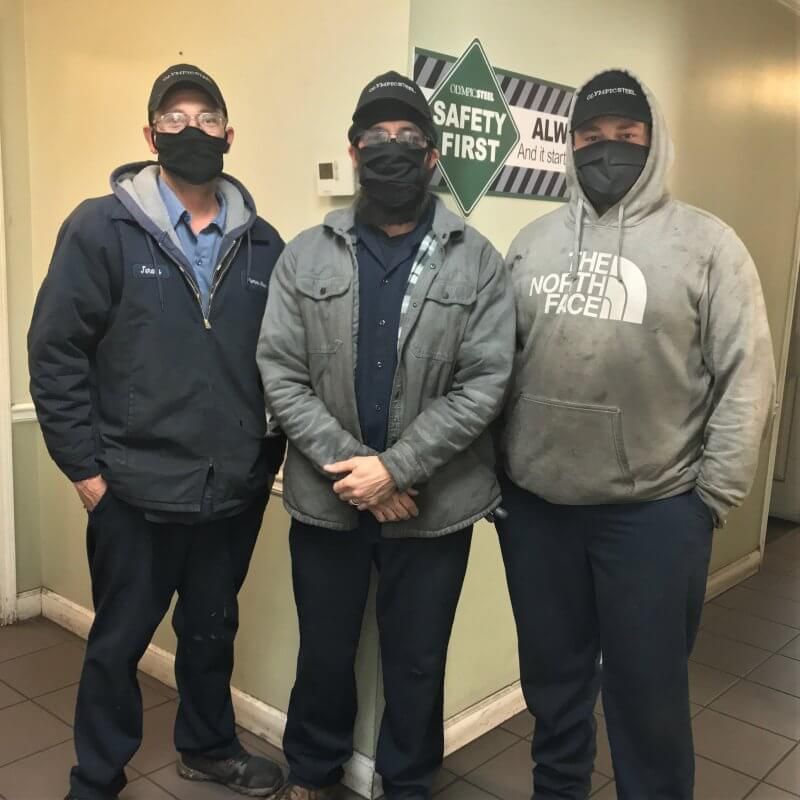
Jeremy Russ (left), Travis Burns (center) and Hunter Bowman (right), Olympic Steel – Winder/Buford, GA
Olympic Steel – Winder/Buford, GA Team: Travis Burns, Jeremy Russ and Hunter Bowman
Packers were manually adjusting the height of the scissor lift table on the metal stamping line. As stack height increased to near maximum, the packer would need to adjust the height before the next blank moved from the conveyor belt to the stack of finished parts.
As output increased, manually adjusting the table height became more difficult to manage safely. Travis Burns (Production Supervisor), Jeremy Russ (Machine Operator) and Hunter Bowman (Machine Operator) identified the issue and brainstormed possible solutions. To eliminate the hazard and address the issue, the team fabricated an adjustable mounting system to position an existing proximity switch linked to the control of the hydraulic scissor lift. When a stack of parts reaches the height established during setup, the scissor lift will lower automatically, allowing the packer to maintain focus on the blanks coming off the conveyor.
Lesson Learned:
Just because machinery comes with the tools we need to complete the job, the tools may not be configured to meet our specifications – it works, but there could be a better, safer way to do the job. As we strive to continuously improve, rethink standard processes to meet our improved productivity and ensure we’re all able to work as safely as possible.