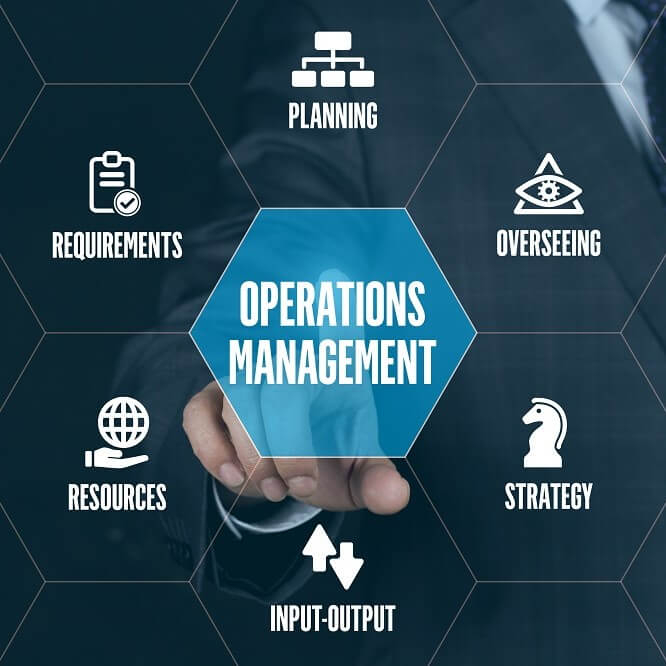
Our Operations Management Team is Growing
Adjusting our operations resources to better meet the needs of divisions, increase efficiencies as an enterprise and develop our operational processes.
In general terms, Olympic Steel’s operational processes are divided into two categories: distribution and fabrication.
Distribution locations are service centers with first stage processes like temper passing, cutting-to-length and slitting. Fabrication locations perform first or second stage processing like laser cutting, forming and welding.
At the divisional level, operations departments are tasked with all aspects of operations – receiving, production, quality, shipping and maintenance. That includes day-to-day operations and long-term projects needed to keep our facilities and machinery in tip-top shape.
It’s no small task for each division to source and manage resources to complete daily operations and upcoming projects at the same time. While there has always been corporate support, there hasn’t always been a team of dedicated resources available to manage divisional projects from start to finish and extend best practices to the rest of the enterprise.
Until now.
Corporate Operations is Growing
Terry Rohde, Vice President – Operations, says, “There are many projects in different stages around the organization – upgrades, repairs, maintenance and purchasing new equipment, for example. To support the divisions, I’m excited to announce two additions to the Corporate Operations Management team.”
- Dan Leas, Corporate Operations Project Manager, joined Olympic Steel in 2011 as the Maintenance Manager for the Integrity Stainless division in Streetsboro, OH. Most recently, Dan served as Operations Manager for Integrity Stainless. He has 30 years of experience in the steel service industry with knowledge specific to upgrading, buying and repairing equipment. Effective January 2, Dan is working with distribution divisions who need to upgrade, repair, maintain or purchase new distribution equipment. In addition, he will also assist divisions who are working to improve efficiencies and establish preventive maintenance or spare parts programs at their facilities.
- Dan Mills, Process Engineer, joined Olympic Steel in 2014 as a Laser Operator for the Olympic Steel division in Winder, GA. He held several positions in the division, including Quality Assurance Technician, APQP Engineer, Quality Assurance Manager, and Process Engineer. Dan has extensive knowledge of lasers and was previously a “superuser” company-wide for programming, operation, maintenance and training. In this new corporate role, Dan will draw upon his nearly 10 years of engineering and project management experience to support fabrication operations across the company.
“We’ve never had someone dedicated to researching, quoting and managing these operational processes – and now we have one person for each operational area of the business,” says Terry.
The Corporate Operations Team also includes Coady Barrie, Corporate Quality Assurance Manager, and Jeremy Miller, Operational Excellence/Lean Six Sigma Black Belt, who both support divisions with their respective areas of expertise.
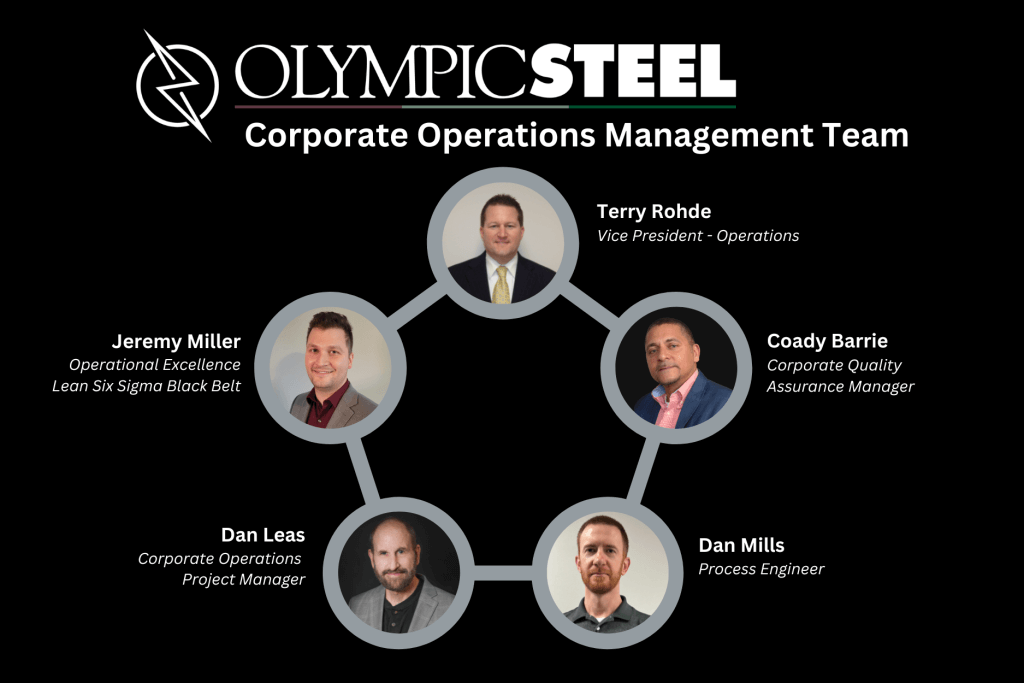
Congratulations to the Corporate Operations Department for the additions to their team, and for adapting to the needs of the business as we continue our work toward safe, profitable growth.
Need Operations Support?
If you have questions about how the Operations Team can help your division with current or future projects, please reach out to Terry Rohde at TRohde@olysteel.com.