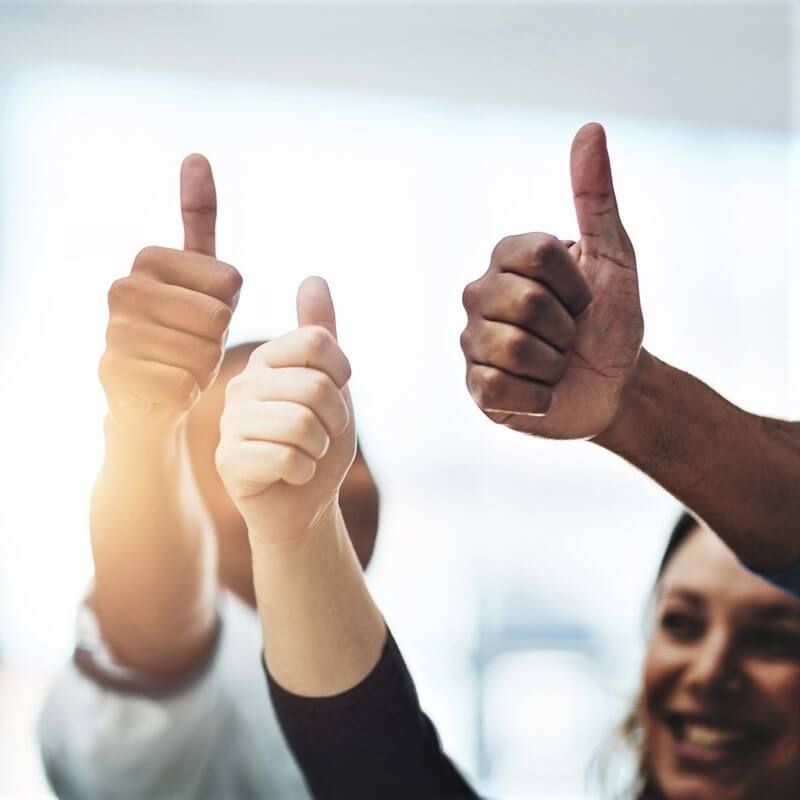
Fe Award of Excellence
Olympic Steel Flawless execution (Fe) Awards
What is Fe?
On the periodic table, “Fe” is the symbol for Iron, the most common element on Earth. At Olympic Steel, Fe is the symbol for Flawless execution, our way of recognizing employee excellence in helping our Company grow safely and profitably.
What is the Fe Award?
Each quarter, Olympic Steel employees are encouraged to nominate themselves or their co-workers to recognize projects and initiatives that accomplish at least one of the following objectives:
- Control expenses
- Perform flawlessly for internal or external customers
- Share best practices across the enterprise
Fe Award Winners receive an award, certificate, gift certificate for branded Company promotional merchandise and a CASH prize. And, we’ve added a new recognition category. Nominees who earn an Honorable Mention will receive a certificate and gift certificate for branded Company promotional merchandise.
Nominate yourself, your team or a colleague now – click here!
The deadline for nominations is the last workday of each quarter. For 4Q 2023, the nomination deadline is Friday January 6, 2023.
Questions?
Want to know more about the program? Contact the HR team with questions at 216.242.2886 (internal extension 19780) or by emailing
Corporate.HR@olysteel.com.
3rd Quarter 2022 Fe Award Winners & Honorable Mentions
Olympic Steel – Schaumburg, IL: Everardo Mendoza
When the Schaumburg division ran out of shrink wrap (needed to prepare finished goods for shipment), Everardo Mendoza, Shop Helper, used the cut ends of PVC film instead. The PVC cut ends are usually thrown away. Instead, the PVC can be used to wrap finished goods, reducing our footprint in the landfills and decreasing packaging expenses by about $5,000 annually. Any division with the same materials could realize similar savings.
Lesson Learned:
How you look at a problem will often determine the outcome – is it holding you back from accomplishing the task or is it an opportunity to do what you need to do in a better way? Everardo saw this issue as an opportunity and found a way to get the job done while reducing waste and expenses.
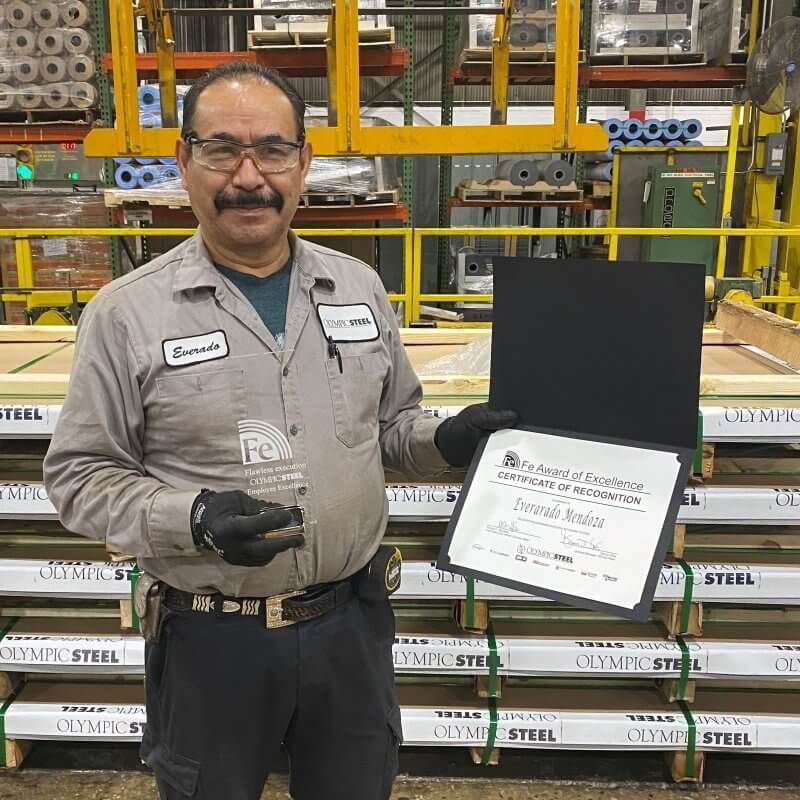
Olympic Steel – Schaumburg, IL: Claudio Rodriguez
Maintaining the PVC inventory at the Schaumburg division can be challenging, especially with frequent supply chain interruptions. Claudio Rodriguez, First Shift Supervisor, recognized the opportunity to improve this process and took action. He worked with Sales and Operations to understand the quantities of PVC needed each month, taking into consideration different sizes and types of PVC used each day. Based on his findings, he determined they needed to triple a usual order to meet their monthly demand. To prepare for the first big order, Claudio worked with the Maintenance department to install additional pallet racks to accommodate the increased volume, labeling the storage area to identify the product. The new process has helped the Schaumburg division maintain an appropriate inventory of PVC. The effort also allowed Schaumburg to supply PVC to some other Olympic Steel divisions that weren’t able to source the material from their suppliers.
Lesson Learned:
Putting in the extra effort and expense helped the division reduce costs and downtime in the long run.
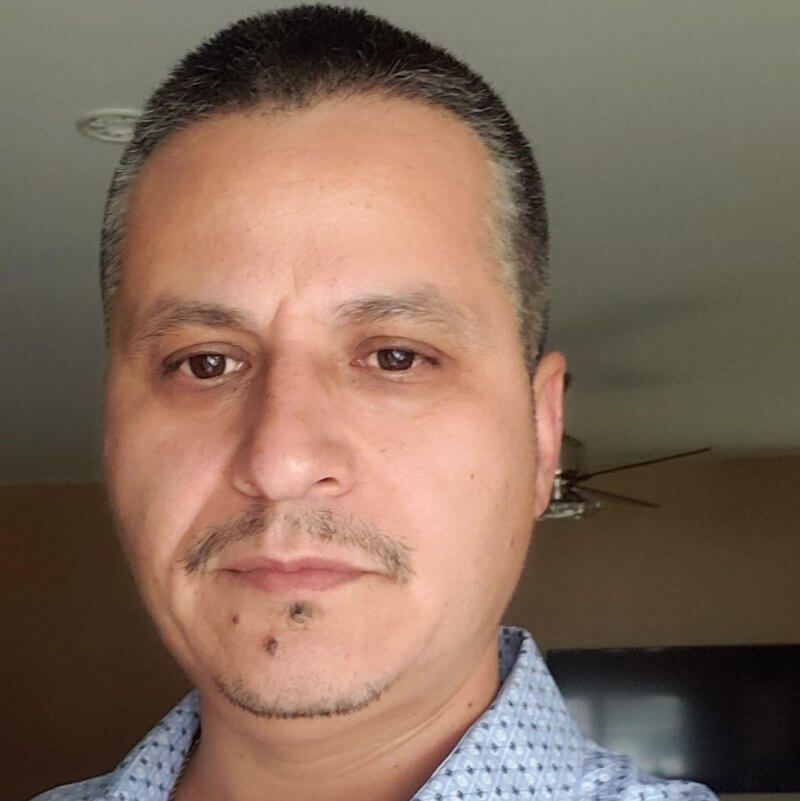
Olympic Steel – Mount Sterling, KY: Bobby (Bo) King
Strengthening our safety culture of learning takes time and requires employees to consciously keep their safety and the safety of others at the forefront of their decisions and actions, every day. Bobby (Bo) King, Senior Production Supervisor, is a leader at the Mount Sterling division for doing just that.
Following Rick Marabito’s CEO Safety Road Show visit to the Mount Sterling division, Tony Dominic, Director – Safety, Health, Environment, noted, “Bo demonstrated exceptional safety leadership. He leads the weekly safety/5S walk and owns the follow-up process. In addition to his operational knowledge, it’s obvious that Bo genuinely cares about the safety of his coworkers. His rapport with his colleagues has resulted in impressive participation from the shop employees. We truly need more leaders like Bo in our operations!”
Lesson Learned:
Recognizing exceptional safety leadership is an important part of developing our safety culture. This one action encourages ownership of safety by the people performing the work and identifies role models for co-workers to emulate.
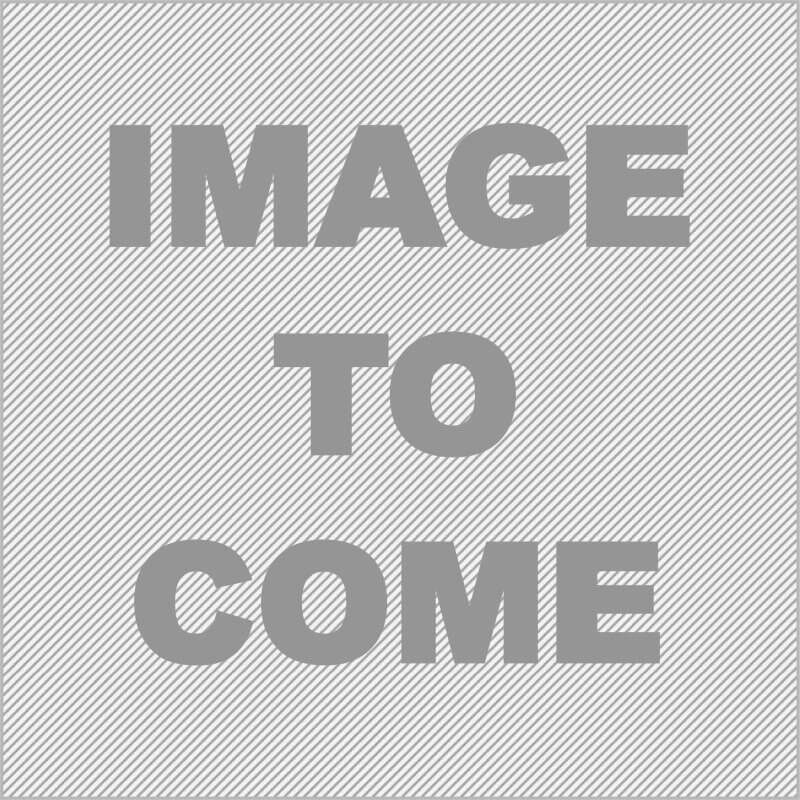