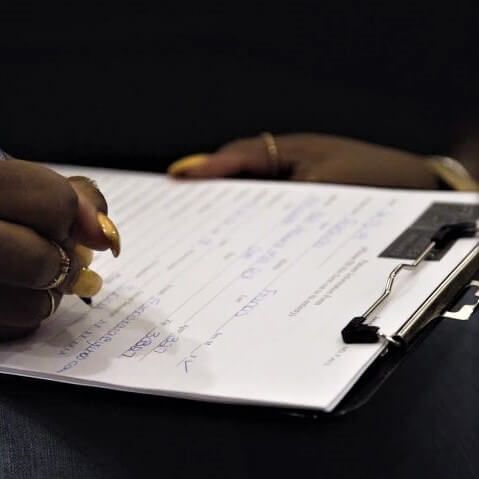
Near Miss Reporting: Why Bother?
Acknowledging situations that could’ve resulted in an accident or injury is an important step in our mission to cultivate a Safety-First culture.
According to the National Safety Council, a near miss is an unplanned event that did not result in injury, illness or damage – but it had the potential to do so. Remember a time when you said, “THAT was a close call!” or “Whew – three more feet and it could’ve ended differently.” When a near miss happens, we need to know about it so that we can learn, improve and hopefully prevent it from happening again.
While most Safety activities are reactive (waiting for an incident to occur before taking steps to prevent a recurrence), near miss reporting gives us a window into what could potentially go wrong in our operations and is an opportunity to get ahead of potential hazards.
Earlier this year, in Safety Stats: 101 on IamOlympicSteel.com, we explained the difference between Leading and Lagging Indicators. Near miss reporting is a leading indicator, a Safety tool used to help avoid errors, reduce risks ans prevent incidents. Here are a few examples of those learning opportunities that near misses create:
- Berlin Metals, Hammond, IN – Forklift driver left their equipment unattended with forks raised, turned on and had not completed the pre-shift inspection. The forklift should never be left unattended when ON, especially with forks raised.
- Olympic Steel, Chambersburg, PA – While performing the routine task of cutting skeleton with an oxy-fuel hand torch, an unnoticed gas leak from the connection ignited. The employee immediately dropped the torch. Maintenance now checks all oxy-fuel hand torches for leaks regularly and prior to use.
- Olympic Steel, Mount Sterling, KY – While trying to transport a drop to the burn table, the plate fell from the magnet causing damage to a bigger magnet. It was determined that the employee attempted to use a magnet that was not designed to carry the weight of the material. Employees must pay attention to the capabilities chart listed on the side of magnets for size and weight ratings.
Thankfully, no one was injured in these instances. And, because they were reported, we have a great opportunity to learn and prevent similar missteps from happening. Sharing these moments can feel uncomfortable, but they are all part of creating a learning culture – one where we collectively share mistakes and solutions with the common goal of keeping our teams safe.
Another type of leading indicator we use at Olympic Steel is a poka yoke. Poka yoke is a mistake-proofing process that also helps reduce risk and prevent incidents from occurring.
In October, we’re kicking off the 4Q Safety Challenge that encourages all employees to share impactful and innovative poka yokes that have reduced our Safety risks in 2021. This challenge is a great opportunity for you to Be a Safety Superhero.
On October 18, we’ll announce contest details. In the meantime, read more about poka yokes on IamOlympicSteel.com.