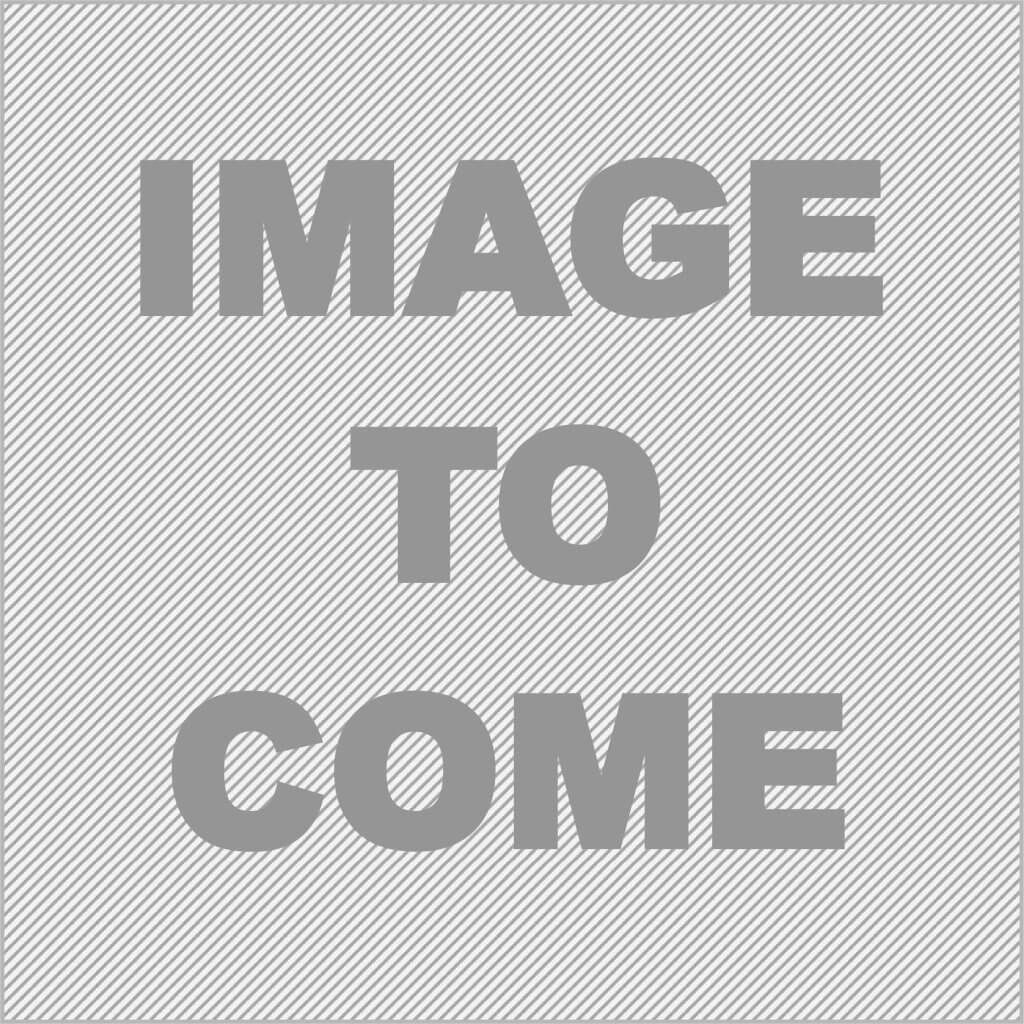
Olympic Steel – Chambersburg, PA Team: Tim Sutton and Ethan Bowers
In Chambersburg’s 1599 building, the set-up of the bay made it difficult to get the necessary equipment into the area for loading or unloading trucks. Loads are frequently transported in and out of the building. Tim Sutton, Production Lead, and Ethan Bowers, Production Supervisor, wanted to overcome this efficiency obstacle, so they created a plan …
In Chambersburg’s 1599 building, the set-up of the bay made it difficult to get the necessary equipment into the area for loading or unloading trucks. Loads are frequently transported in and out of the building.
Tim Sutton, Production Lead, and
Ethan Bowers, Production Supervisor, wanted to overcome this efficiency obstacle, so they created a plan to make it happen. They rearranged and reorganized the area. Then, the team moved 50 bulk storage racks to make the area safer and more efficient. This project eliminated multiple pinch points (potentially caused by the tight fit for material and equipment in the area) and hazards. In addition, it cut loading time by ten minutes per load, saving around 1 hour per day (252 hours per year).
Lesson Learned:
Instead of working around an issue just to get the job done, take the time to figure out if there’s a better way to do it. There may be extra steps in advance to prepare, but the end result will be a more efficient, safer process.