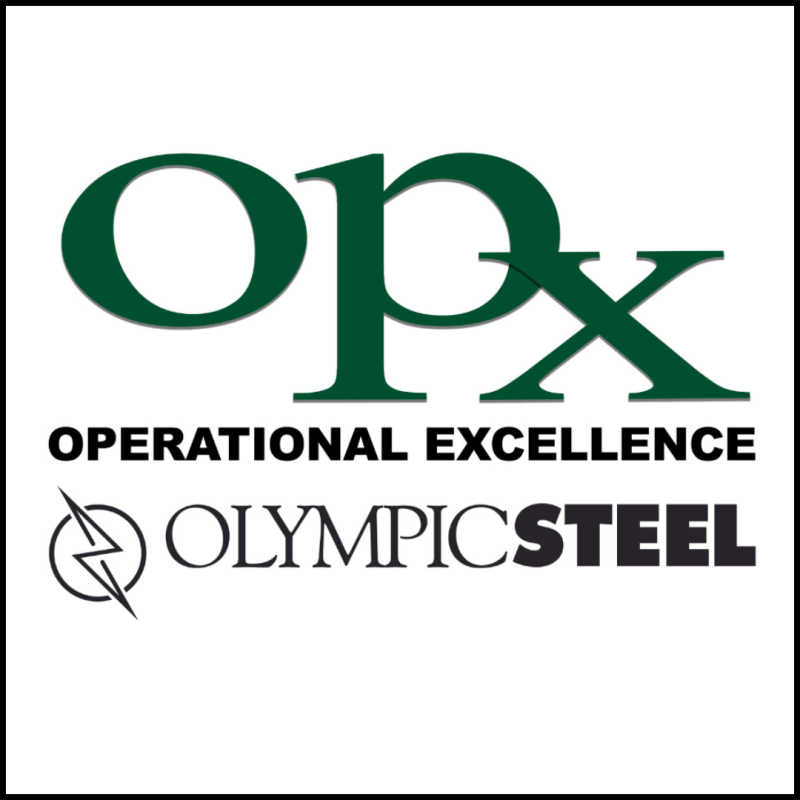
Continuous Improvement Board Keeps Projects Moving
The Operational Excellence Team sets the bar high for organizing tasks and communicating progress with employees. Here's one example of how they do it.
The Operational Excellence Team sets the bar high for organizing tasks and communicating progress with employees. One of the best examples of this is the Continuous Improvement Board that tracks action items.
Robert Erion, EHS Manager and Project Manager, says “This board is how we track continuous improvement activities as well as Human and Organizational Performance (HOP) action items that come from the learning teams that we conduct. It connects the progress of the learning team members to all employees – showing exactly where we’re at with assigned tasks.”
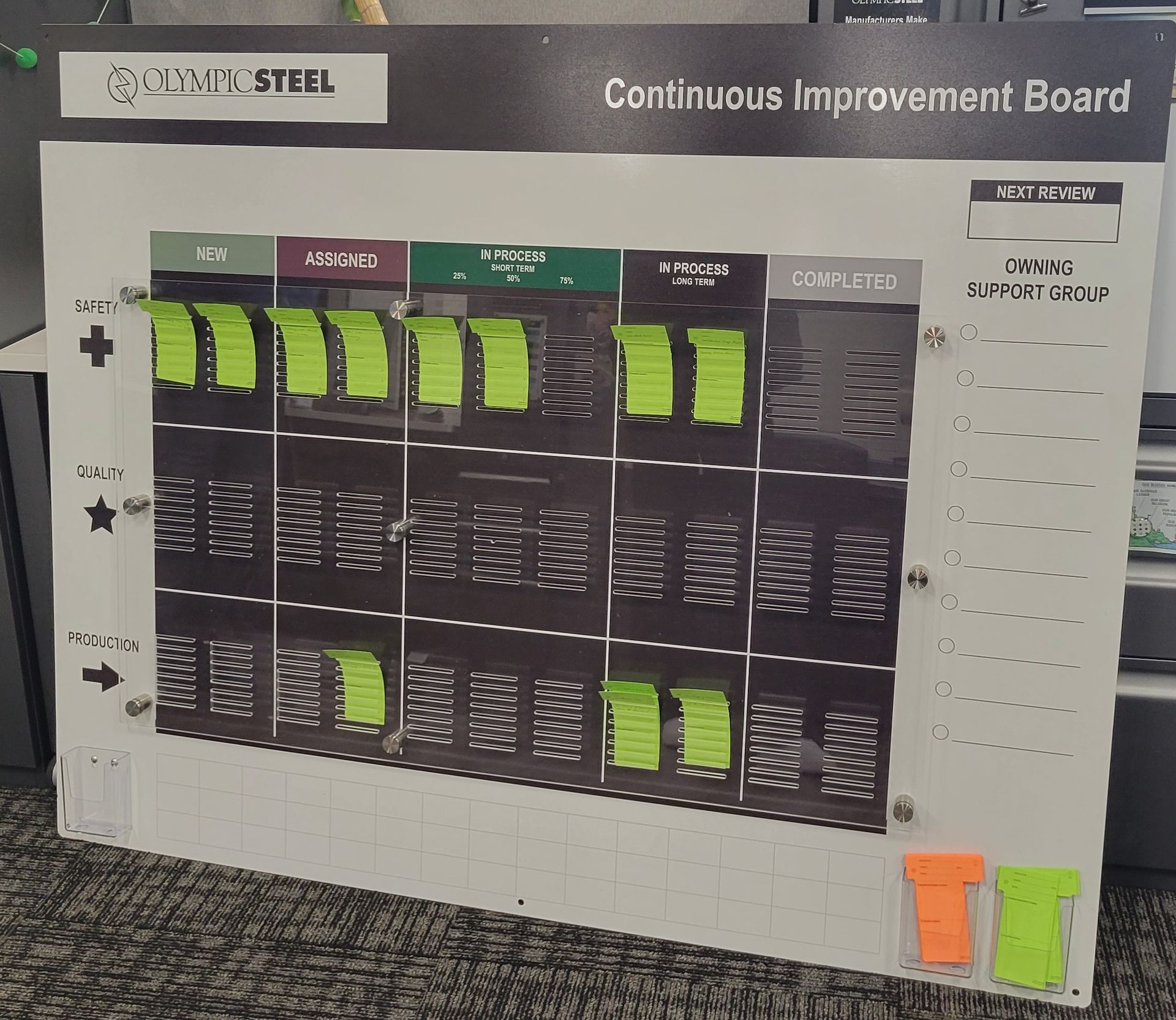
A team that includes Production Supervisors, Plant Manager, Operational Excellence and EHS (Environmental, Health and Safety) meets weekly to discuss the status of each action item (represented by a card). Each card has a colored dot to identify who owns that action. The cards move from new to assigned, to in process to complete. When a task is completed, the card remains in the completed slot until it is reviewed with the employees. That happens in the value stream meetings. After the completed task is reviewed by employees, it’s removed from the board.
Tracking this information visually makes it easy to see where a task is in the process and lets employees know who to contact for anything related to the task.
If you’re interested in learning more or implementing a Continuous Improvement Board at your division, please reach out to one of our experts:
Robert Erion
EHS and Project Manager
763.847.9858, internal extension 71444
Will Robbins
Project Analyst, Sr.
763.542.4882, internal extension 70412