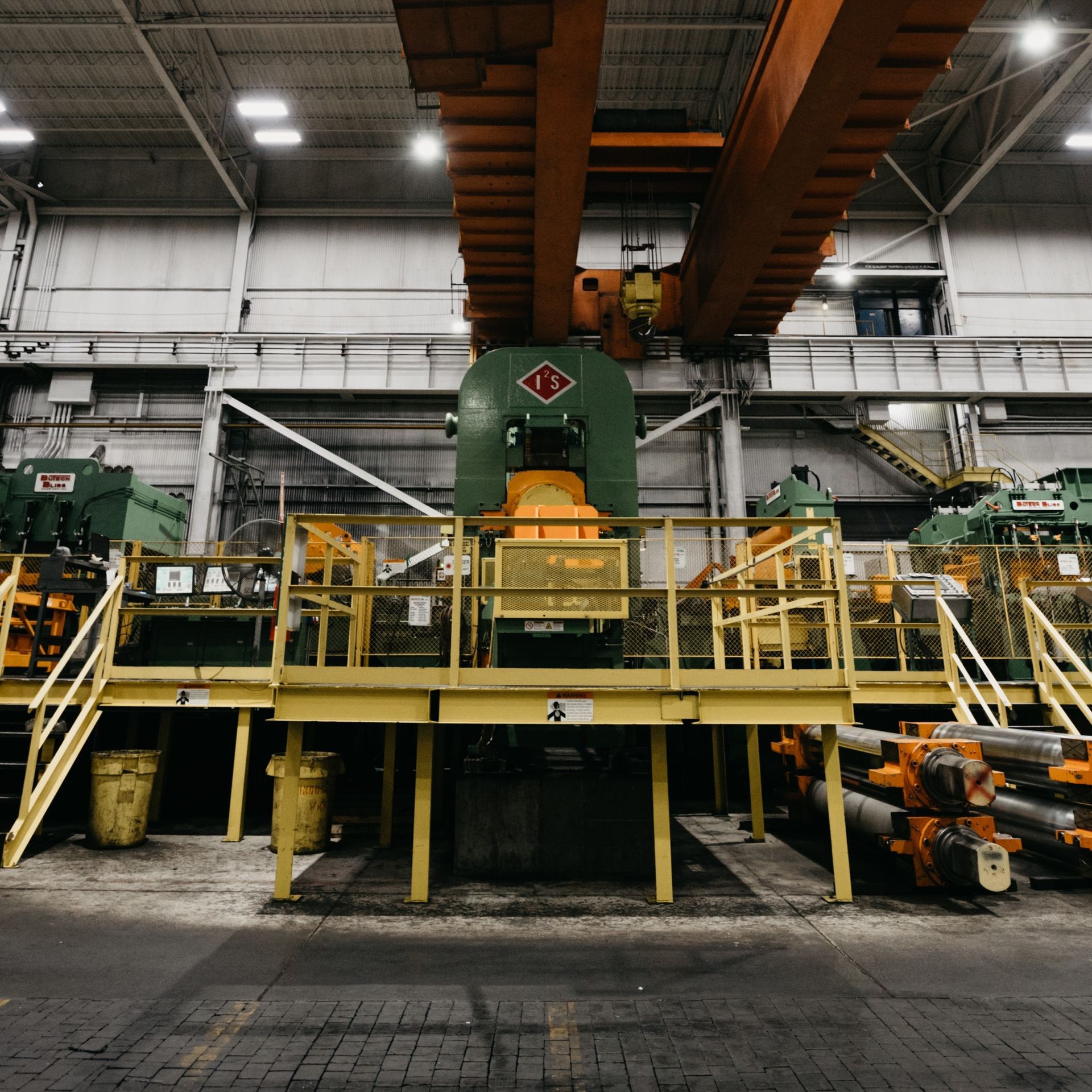
Operations Overview
Olympic Steel’s Corporate Operations Team manages facilities, equipment and processes to enhance efficiencies, improve systems and operate safely.
DIVISION OPERATIONS
A broad definition of what our operations teams do includes the activities inside facilities that receive, process and ship product to our customers. Operations is connected to every facet of the company. At Olympic Steel, our Local/Division Operations Teams support almost 50 facilities and more than 350 pieces of equipment, run by nearly two-thirds of our employees.
Sourcing and managing resources for safe day-to-day production, including appropriate staffing levels, employee training, first stage and fabrication processes, delivery of high-quality products and essential ongoing projects, like preventative maintenance, facility maintenance and repair, and new equipment installation are the main focus of our Local/Division Operations Teams.
FABRICATION
Fabrication services include value-added processing such as laser cutting, machining, forming, welding and assembling, and are also an essential function of operations. Our Corporate Fabrication Team partners with our outside sales teams in every region with a focus on growing the fabrication business, utilizing existing equipment across the Company. If a project exceeds the capabilities of existing assets, the Corporate Fabrication Team will work with the Corporate Operations Team to decide if new equipment is needed. Click here to read more about Olympic Steel’s Fabrication Team.
CORPORATE OPERATIONS
Operations at the corporate level is a dedicated, shared resource that guides and partners with Local/Division Operations Teams in determining needs and finding solutions to help gain efficiencies and improve processes, with the goal to increase production. The Corporate Operations Team supports plants, property and equipment across the enterprise and utilizes Operational Excellence (OpEx) and Lean Six Sigma methodologies to improve processes, reduce costs and maximize productivity.
When a plant has a process they want to improve, the Corporate Operations Team can support with expertise, enterprise-wide resources and vendor management. Researching and making recommendations, assistance in submitting capital expenditure requests, and guidance in purchasing new equipment are fundamental pieces of the Corporate Operations Team’s role. At any given time, the Corporate Operations Team has between 10 and 15 ongoing projects with many moving parts, some of them requiring project management to oversee the process. The Corporate Operations Team also offers a broader perspective of the organization to help share best practices, capitalize on processing redundancies (that is, taking advantage of where we offer the same processing capabilities in multiple locations) and connecting subject matter experts across the Olympic Steel enterprise to tackle challenges or simply help each location run at its best.
OPERATIONS MANAGEMENT
The Corporate Operations Team is led by Terry Rohde, Vice President – Operations, who has been with Olympic Steel since 2001. He has a degree in engineering and has held positions across multiple divisions, including Operations Manager, Sales Manager, General Manager and Director of Operations.
The Corporate Operations Team is comprised of the following members:
- Dan Leas, Corporate Operations Project Manager – works with divisions in upgrading, purchasing and repairing equipment such as cut-to-length lines and slitters. He also has expertise in facility repairs, crane maintenance, efficient plant design and distribution.
- Dan Mills, Process Engineer – supports and focuses on all laser and fabrication operations and equipment, including efficient plant design and operator training.
- Jeremy Miller, Operational Excellence/Lean Six Sigma Black Belt, Process Engineer – focuses on and manages processes for plasma cutting and fabrication equipment, including efficient plant design and machine utilization.
- Coady Barrie, Corporate Quality Manager – assists all divisions in maintaining their current quality certifications, along with improving their processes and helping those who need a new customer required certification.
OUTLOOK
The Corporate Operations Team works with General Managers, Regional Vice Presidents, Operations Managers, Quality Manager and Safety Managers in the divisions to make sure they have the right equipment and are operating as efficiently and safely as possible. This will allow the Company to continue to grow profitably, and explore new opportunities as improved technology, value-added processes and fabrication opportunities arise.
To learn more about Olympic Steel, visit olysteel.com.